ABSTRACT
The demand for batteries for energy storage is growing with the rapid increase in photovoltaics (PV) and wind energy installation as well as electric vehicle (EV), hybrid electric vehicle (HEV) and plug-in hybrid electric vehicle (PHEV). Electrochemical batteries have emerged as the preferred choice for most of the consumer product applications. Cost reduction of batteries will accelerate the growth in all of these sectors. Lithium-ion (Li-ion) and solid-state batteries are showing promise through their downward price and upward performance trends.
We may achieve further performance improvement and cost reduction for Li-ion and solid-state batteries through reduction of the variation in physical and electrical properties. These properties can be improved and made uniform by considering the electrical model of batteries and adopting novel manufacturing approaches. Using quantum-photo effect, the incorporation of ultra-violet (UV) assisted photo-thermal processing can reduce metal surface roughness.
Using in-situ measurements, advanced process control (APC) can help ensure uniformity among the constituent electrochemical cells. Industrial internet of things (IIoT) can streamline the production flow. In this article, we have examined the issue of electrochemical battery manufacturing of Li-ion and solid-state type from cell-level to battery-level process variability, and proposed potential areas where improvements in the manufacturing process can be made. By incorporating these practices in the manufacturing process we expect reduced cost of energy management system, improved reliability and yield gain with the net saving of manufacturing cost being at least 20%.
PROBLEM DEFINITION
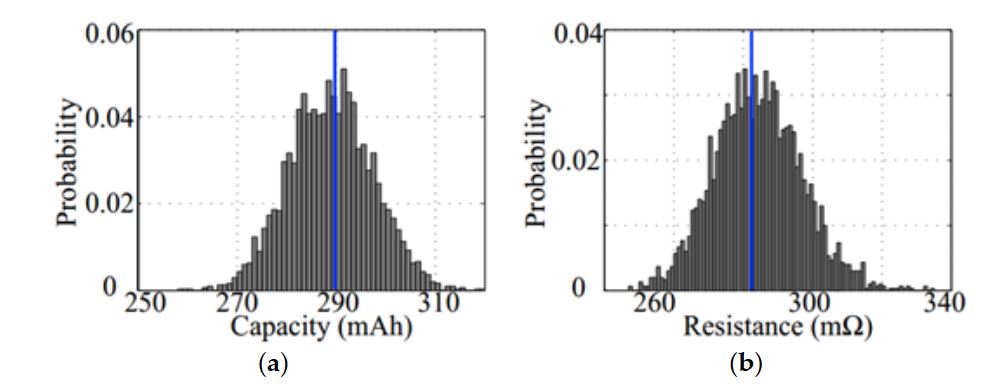
Figure 1. Probability distribution of the (a) cell capacity and (b) resistance profile of the sample cells
As stated before, the PV industry has made immense improvements in processing by adapting many well-known practices from the semiconductor industry. The battery industry can also adapt some proven practices and processes from PV and semiconductor industries. In this article, we will refer to an individual electrochemical or solid-state cell as “cell”. When several such cells are combined together, it will be referred as “battery pack”, which may include the battery management system (BMS) with sensors, controllers, processing unit, etc. On many instances of real life application, cells may be arranged according to the need to achieve a desired voltage level and capacity. Figure 1 shows a statistical distribution of cell performance for Li-ion cells in terms of capacity and resistance.
PROPOSED CHANGES IN LITHIUM-ION BATTERY MANUFACTURING TO ADDRESS PROCESS VARIABILITY
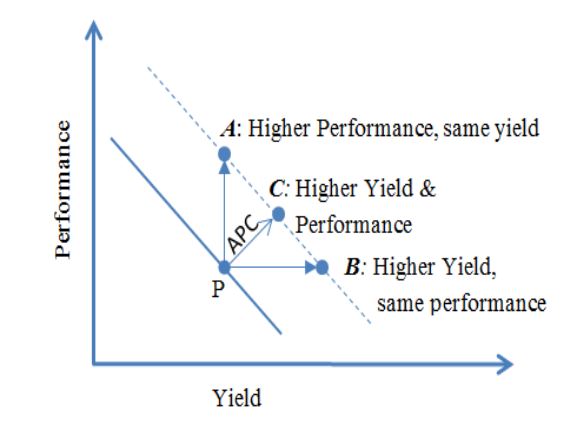
Figure 3. Shifting a simplified yield-quality line with the use of advanced process control (APC)
Based on concepts discussed, we can consider a simplified case of the qualitative relationship between yield and performance, as depicted in Figure 3. The current production point “P” is on a line that defines a simplified linear relation (with negative slope) between yield and performance. In the real world, such simple correlations may not exist, but this simple, linear relation is sufficient to illustrate the point being discussed. Along this line, an increase in either production or performance will sacrifice the other. In other words, if the allowed window for quality is narrow, more products will have to be discarded. Consequently, the yield will decrease. Similarly, if more products are passed as acceptable, then the overall quality will be compromised.
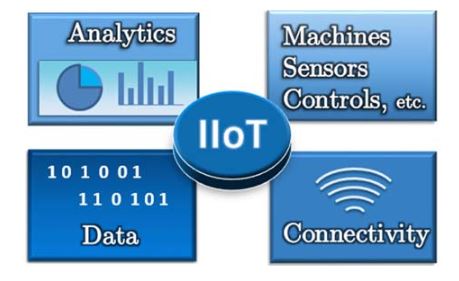
Figure 7. Industrial internet of things (IIoT) framework that utilizes connectivity, data, and analytic tools to communicate effectively with machines
Due to adequate data gathering through IIoT, many potential problems can be detected at an early stage of manufacturing. The early detection of manufacturing problems can lead to corrective measures saving wastage in discarded products, compensation, product recalls, etc. The data gathered through the IIoT platform can point out inefficiencies and problems at a faster pace, save time and money and support an integrated business intelligence approach. In conventional manufacturing, a quality check of the finished product may reveal defects and then corrective actions may be initiated by a human operator.
DISCUSSION
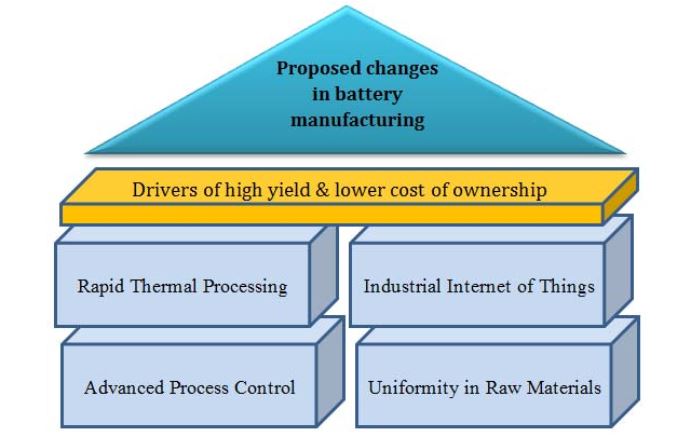
Figure 8. Proposed changes and their impact to bring down cost of ownership (COO)
The steps proposed in this paper would increase the throughput, yield and material utilization and decrease the battery manufacturing cost, due to higher yield. Thus, the net result will be reduction of COO. With incorporation of all the proposed changes, we expect to manufacture higher quality batteries at a cheaper cost. All the proposed changes are presented in concise graphical form in Figure 8.
CONCLUSIONS
Process variation in manufacturing is one of the key factors that reduces optimal battery performance and leads to higher manufacturing cost. There is room for improvement in controlling the process variations observed in battery manufacturing. In this paper, we have emphasized that the variation from cell-to-cell is crucial for energy storage application. The SPC used currently by battery manufacturers should be replaced by APC to gain better control over the manufacturing process. The use of RTP in place of CFP is suggested in all thermal process steps to reduce process variability and improve the performance and reduce cost of batteries.
IIoT has the potential to manage manufacturing in a more efficient and agile manner. Besides research in materials and chemistry, these steps can help a manufacturer to produce in an efficient way while delivering the best quality product. The battery industry needs to act quickly to be prepared for the future when battery storage plays a very important role in stationary applications for power storage, as well as in EVs used in the surface transport sector.
Source: Clemson University
Authors: Amir A. Asif | Rajendra Singh